The Quiet Guardians of Aerial Lift Safety
When we talk about aerial work platforms (AWPs), boom lifts, or scissor lifts, the key safety components typically fall under the areas of structural integrity, hydraulics, fall protection equipment, and tires along with the prominent scissor lift sensors and scissor lift spare parts.
In the long list of touchpoints, the platform controls and scissor lift sensors remain in the dark, and they actually are responsible for the light yet important tasks of making sure every move is accurate, every single rise is safe, and every landing is wanted and completely under control.
According to some industry resources like scissorlifts.org, the main cause of many accidents is not major problems with the mechanical system regarding scissor lift spare parts, but the fact that the electronic entities that were in charge of the safe conduct of the machine were left unchecked or not properly maintained, hence the results.
The most common scissor lift spare parts are unwanted movements, wrong height changes, or the stopping of the entire machine when it is vitally important to the operation.
This post will demonstrate how these hardly noticeable sections—platform’s brain and nervous system—are, in fact, the main participants in the fastest, safest, and most productive operations and also that if these are disqualified, severe repercussions can be the result.
Why Platform Controls & Sensors Are Often Overlooked
The control and safety of a machine in the AWP industry meet as the main godfather and the other as most capable sector of executing possible actions is a touching example of high teamwork.
Thus, sensors and controllers are viewed as accessory parts as the most likely scenario until they break down.
Reasons for being overlooked include:
- Small and internal components: Just as sensors are more obtrusive than hoses, they are also less conspicuous during a walk-around check of a machine.
- Low maintenance awareness: Many mechanics and operators often give more attention to the checking of only the mechanical parts but not the electrical parts.
- Intermittent failure: It is quite normal that the sensors and control modules can become a little worse every day such that their faults are very difficult to detect.
Consequences of Overlooking Controls & Sensors:
- Unexpected machine shutdowns
- Failure of emergency stop functions
- Tilt or overload sensors not engaging
- Poor response from joysticks and directional controls
Key Platform Controls & Their Safety Role
Control modules are the relationship frontend between the operator and the machine. It is definitely the best option at the moment. including joysticks, keypads, selector switches, and emergency stops.
Critical components to monitor:
- Joystick controllers: Determine platform motion and direction.
- Key switches and lockouts: Prevent unauthorized or unsafe operation.
- Emergency stop buttons: Instantly disable the machine in case of error.
Control Component | Common Issues | Safety Impact |
Joystick | Loose wiring, wear & tear | Unintended movement or unresponsiveness |
Emergency Stop | Dirty contacts, stuck buttons | Failure to stop lift in emergency |
Toggle/Key Switch | Corrosion, broken contacts | Inability to power machine on/off |
You may not be aware of the fact but it is quite possible that ignoring the maintenance of these parts of your lift is the main reason for having an unpredictable behavior, which can, in turn, pose danger not only to the operator but also to the people within the lift and around it.
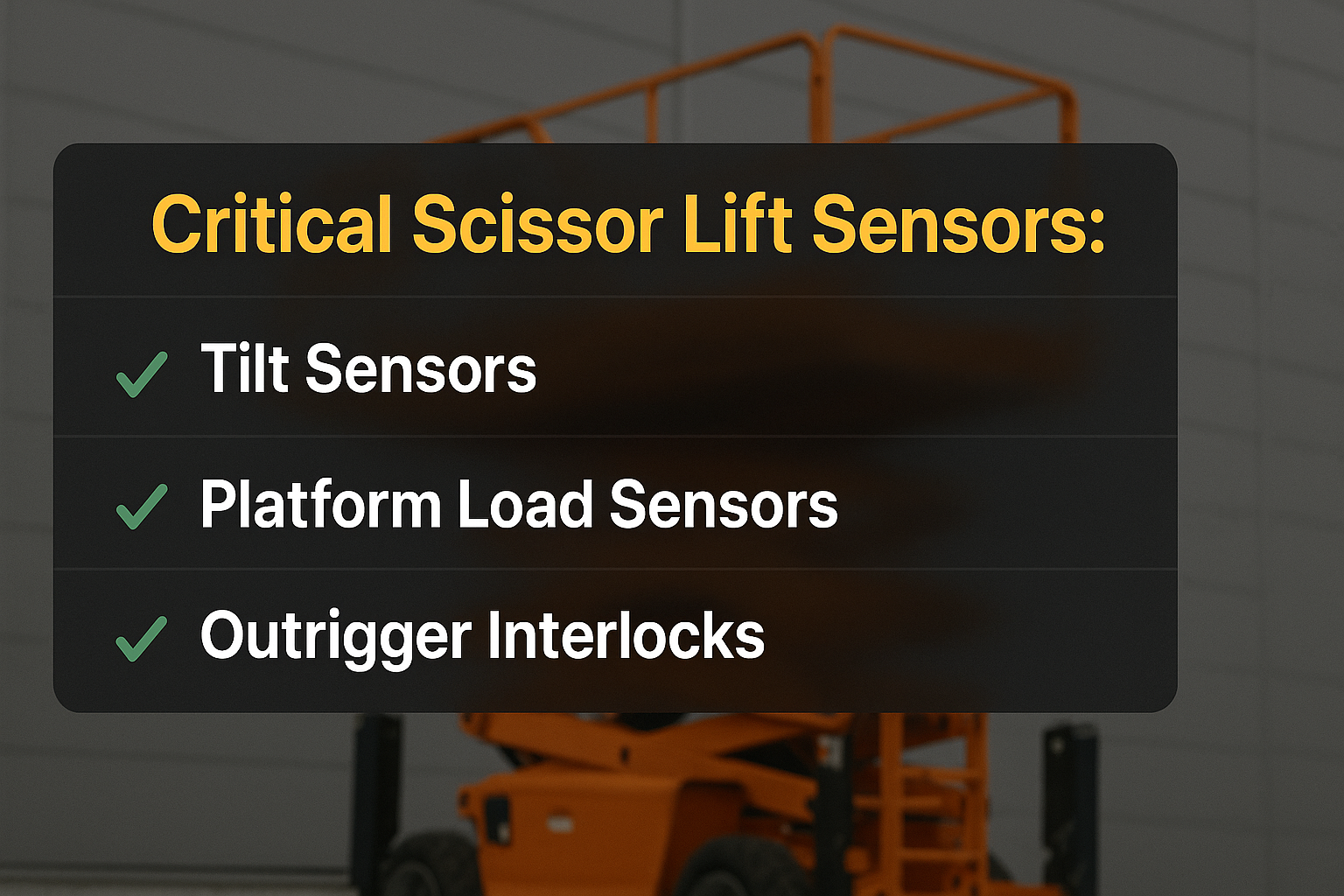
Critical Scissor Lift Sensors That Impact Safety
These devices work as the eyes and ears of the machine. They sense tilt, pressure, position, load, and environmental conditions so that it is certain that the entire system is within a safe operating limit.
Must-try sensors for high-priority cases:
- Tilt Sensors: Halt lifting process regardless of the ground’s condition.
- Platform Load Sensors: Indicate an excess of load in the platform.
- Outrigger Interlocks: Make the lift inoperative when outriggers cannot be deployed properly.
All these scissor lift sensors are part of the programmable control system of the lift. If tilt sensor is broken, then it becomes suitable for it to:
- Be operated on if it is the cause of the fault (if failed “open”), or
- Be totally safe in operation (if failed “closed”).
Give Attention to Scissor Lift Sensors Problems:
- Wiring that becomes either loose or unconnected
- Light sensor drift from normal or proper settings
- Rusted parts that affect the connecting areas
Sensor Type | Location | What It Prevents |
Tilt Sensor | Under platform base | Tipping over on slopes |
Load Sensor | Beneath platform floor | Overloading and component stress |
Pressure Transducer | In hydraulic circuit | Overpressure situations and blowouts |
Travel Sensor | Boom/scissor linkage joints | Incorrect positioning or limits breached |
Unseen Dangers Brought by Scissor Lift Sensors & Control Failures
However, the problem with the electronic components is that failures might not be clear at the first sight. In sight, you can see the break of a mechanical part, but a loose joystick cable? Not really.
Potential risk of non-working systems:
- Wrong sense of safety: The personnel can be deceived by the interlock sensors to believe that the outriggers are actually stable.
- Ghost movements: Due to a shorted or misaligned joystick, the uncommanded moving of equipment can occur.
- Bypassing faulty systems: By using the example of an item not functioning properly, The situation is not uncommon where engineers directly deactivate the sensors to allow for their system’s execution; thus this process will invalidate the whole safety clemency.
In those cases, where outdoor lifts are used, the situation can get much worse. It’s enough for a lift to be exposed to temperature changes, moisture, or vibration, and all these conditions can accelerate electronic components’ wear.
Regular Maintenance for These Vital Systems
The platform controls and sensors do not require much more mechanical replacement, but they definitely need periodic checks, tests, and electrical purification.
Suggested guidelines Regarding Scissor Lift Spare Parts:
- Weekly function tests: Every sensor, button, and switch should be in use and test it before using it.
- Electrical contact cleaning: You should use dielectric grease in order to protect the parts against corrosion.
- Regular calibration checks: Especially for tilt and load sensors.
- Record-keeping: It is important that you keep a good record of the items and when they were inspected and/or replaced.
Maintenance Task | Frequency | Tool Needed |
Sensor function test | Weekly | Multi-meter / Diagnostic |
Joystick feedback check | Monthly | OEM diagnostics tool |
Emergency stop verification | Weekly | Manual operation |
Wire harness inspection | Monthly | Visual & probe test |
One of the reasons that scissor lift sensors and control modules are usually left out is that they are rarely kept in stock at construction sites. In fact, these are usually non-standard spare parts in most maintenance programs.
The significance of stocking control & Scissor Lift Sensors and Spare Parts:
- Downtime cost: Stopping projects for a sensor delivery can cause a loss of thousands of dollars.
- Safety mandate: Most authorities around the globe impose safety regulations on MEWP machines by requiring companies to maintain the entire safety system intact all time.
- Operator trust: Part of the confidence of technicians comes from the availability of the “big” spares right away.
Recommended Inventory of Scissor Lift Spare Parts:
- Joystick assemblies
- Tilt sensor kits
- Emergency stop switches
- Load cell or platform pressure sensors
- Key switches / ignition modules
Scissor Lift Sensors Safety Guidance:
In particular, potential threats to work safely at heights and to avoid AWP hazards are typically minimized by scissorlifts.org through constant reminders about the significance of preventative maintenance.
In addition to that, the site content features regular alerts on product recalls and safety advisories, warning users of possible issues with control modules or sensor errors.
Implementational recommendations from scissorlifts.org:
- There is no way you will ignore sensors because they are broken.
- Replace parts with original, not with those of third-party.
- Keep the control modules’ software/firmware up to date from time to time.
- Conduct the checks based on the requirements set in the ANSI A92.20 standard.
By following the above guidance, one can not only improve safety but also make sure that the lift operations performed are OSHA and ANSI compliant.
FAQ’s
Q1. What are the possible consequences of the non-functioning tilt sensor in a scissor lift?
By having a tilt sensor that is non-functional, you could put the machine at risk of unsafe slopes and cause a rollover. When operated in “locked” mode it will block all movements, therefore, delays may occur. It is necessary to perform regular checks.
Q2. Is it acceptable to go on using a sensor that is not working as required?
No. It should be noted that according to scissorlifts.org and the standards of ANSI, bypassing the sensors is the act that makes the operation unsafe and hence, it may also make the operator liable.
Q3. How frequently should the platform sensors be checked?
It is recommended that you should carry out a monthly calibration of tilt and load sensors, or, alternatively, check the sensors immediately after noticing anything unusual. For some models, you may need to use diagnostic tools which are -specific.
Q4. What is the cause of the sporadic malfunctioning of my joystick?
The main reasons for the failure to operate that stick are the wires, the internal wear, or the lack of a signal from a board. Depending on the fault, one should replace or adjust it.
Q5. Is an E-stop switch a spare part?
In general, yes it is. E-stop switches wear out, and it is recommended to substitute the one that is sluggish, dirty, or unresponsive. Also, it is advisable to keep one in reserve.
Q6. How do I identify sensor-related failures in lifts?
Contemporary mobile elevating work platforms (MEWPs) frequently display trouble codes as an initial recognition of the cause. Besides, the user can use the OEM manual or a diagnostic tool to identify a break.
Q7. Where can I buy genuine platform controls and sensors?
It is highly recommended to always go for OEM suppliers or vendors who have been referred to the resources like scissorlifts.org. Generic components might not fit properly or be safe.
Conclusion: Scissor Lift Sensors – A Small Part with a Huge Role
Despite the fact that hydraulic rams, outriggers, and batteries typically get the most attention, platform controls and sensors are actually the ones that could be the difference between safety and danger during a workday. They are relatively small, and their being stowed away from sight can facilitate the forgetfulness of their existence by those in charge, but the consequences of such ignorance can be overwhelming.
Irrespective of whether you are controlling a number of lifts or are in charge of a single scissor lift, making a point to perform regular sensor check-ups and proper control module maintenance of scissor lift spare parts and scissor lift sensors then, in the end, will lead to your compliance, increased productivity and, of course, to the priority of operator safety.